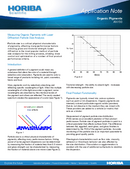
A broad collection of pigment, powder coatings, and ink products exist in particulate form in both the raw materials and finished products. The particle size distribution of these materials determines their appearance, quality, functionality and processability. These samples cover an extremely broad range of size distributions. This is probably why HORIBA laser diffraction particle size analyzers have always been the system of preference in these industries. The LA-960 Particle Size Analyzer has a dynamic range of 10 nanometers – 5,000 microns which makes it uniquely flexible to measure everything from sub-micron pigments like carbon black and TiO2 to large organic pigment powders.
Titanium Dioxide (TiO2) is a pigment used in paints and many other applications. The particle size distribution of titanium dioxide is critical because it affects many important physical properties that influence final product performance. The particle size analysis is typically performed using the laser diffraction technique, and specifically by the LA-960 system, at dozens of TiO2 manufacturing sites around the world.
Overlay of wet slurry and dry powder titanium dioxide measurements with the LA-950.
Particle size is a critical physical characteristic of pigments, affecting many performance factors including gloss and tinctorial strength. Laser diffraction is the most popular method of particle size analysis for the milling process, allowing close control and optimization of a number of final product performance criteria. A study was performed on four organic pigments (2583 Diarylide Yellow 83, 1274 Hansa Yellow 74, 2574 Hansa Yellow 74, and 5576 Phthalo Blue 15:3) using the LA-960 PowderJet dry measurement accessory to optimize a method and test reproducibility.
Particle size is directly related to hiding power in pigments. Due to its speed and wide size measurement range, laser diffraction is an ideal tool for tracking the grinding process and therefore controlling the resulting pigment performance. Laser diffraction results rapidly tell the manufacturer when a product is sufficiently small and therefore allows optimum use of manufacturing equipment.
Plot of hiding strength and geometric mean particle size as a function of grinding time.
Powder coatings are alternatives to paints that are comprised of a resin and a pigment. The powder is sprayed on the part and attracted by the electrostatic charge applied to the part. The item is then heated in an oven to cure the resin and form a solid layer. Particle size is important to provide the optimum surface finish and minimize process waste. As with other pigments, the size of the largest pigment particles affects the surface finish. Larger particles will protrude above the surface, leaving a rough texture. Because powder coatings are applied with spray guns, similar to paint, large particles can clog the spray nozzle orifice.
Synthetic iron oxide powders are used primarily for their pigmentary and magnetic properties (although not all types of iron oxide are magnetic). Iron oxide powders are the most widely used of all colored inorganic pigments, used in concrete products, paints, plastics, and other media. Due to their chemical and magnetic properties, iron oxide powders also find significant commercial usage in electromagnetic components, catalysts, toners, magnetic recording media, and other applications.
Inks are a liquid dispersion of pigments for writing or printing. The product is a mixture of a number of components, the majority being the pigment particles in some liquid carrier. A number of additives are usually included to modify viscosity, drying, stability, or color characteristics. Particle size of the pigment particles can significantly affect the color strength, surface finish, and durability of the final product. In addition, the particle size of the pigments must be small enough that they do not block the nozzles of the printing mechanism.
Inks may require either water or an organic solvent dispersant, and sometimes a surfactant .The refractive index depends on the pigment used. Ultrasound is typically not required for a well formulated, stable ink. These submicron dispersions are ideal samples for the LA-960 Particle Size Analyzer since it possesses the best nanoparticle performance on the market. The result shown below with a Dv50 of 106 nm doesn’t even come close to the low end size limit of the LA-960. See the test method on measuring 30 nanometer LUDOX TM.
Chromium oxide is a green material. The dimethicone treatment adds a degree of “slip” to the particles allowing for better color saturation. The resulting green pigment is predominantly used in cosmetics manufacturing.
This sample was slightly hydrophobic, so Micro-90 surfactant was used to wet a small amount of sample in a beaker. The dispersant used was water with 0.1% sodium pyrophosphate. The result from this analysis is shown below.
Laser Scattering Particle Size Distribution Analyzer
Dynamic Image Analysis
Direct Imaging Particle Analyzer
Nanoparticle Analyzer
Centrifugal Nanoparticle Analyzer
Laser Scattering Particle Size Distribution Analyzer
Laser Scattering Particle Size Distribution Analyzer
Static Image Analysis System Particle Size
BET Flowing Gas Surface Area Analyzers
BET Surface Area Analyzers
Simultaneous Multi-Laser Nanoparticle Tracking Analysis (NTA)
Do you have any questions or requests? Use this form to contact our specialists.